FOUNDRIES
Continuous flow cooling
of truck engine blocks
JOEST delivers Casting Cooler to motor block and eylinder head foundry.
The Casting Cooler cools these motor blocks from 400 °C down to 100 °C. A radiation pyrometer measures the temperature of the parts.
This year, JOEST manufactured a 42-meter-long Casting Cooler for a client. The cooler was designed as a mass compensated resonance machine for the shock-free cooling of truck motor blocks in a continuous production flow. It is located after a green sand molding plant that produces 60 parts an hour with a weight of up to 550 kg per piece. The Casting Cooler cools these motor blocks from 400 °C down to 100 °C. A radiation pyrometer measures the temperature of the parts.
From a machine dynamics standpoint, the Casting Cooler is equipped with active, synchronized vibration dampers. They are sub resonantly harmonized and feature an eccentric slider-crank drive. Open at the feed and discharge ends, the machine has a near airtight hood that forms an ideal flow channel. The air injection nozzle creates a strong air flow through this channel. The counter flow principle enables a direct convective heat exchange between the casting parts and the cooling air, resulting in a shock-free cooling process. The preheated air that has already passed by several parts reaches the hottest casting parts at the hot feed end of the cooler. Pulse-width modulated water injectors regulate the moisture of the processing air. JOEST designed the optimal solution for this client by considering the entire process including an air-cooling system and planning the machine accordingly. The design was tested for its operational safety using a precise calculating tool. This enabled our engineers to achieve the best possible level of efficiency. Furthermore, the machine is equipped with very reliable modules such as the damper stations and only transfers small residual forces into the foundation. Natural flexural frequencies do not occur within the system and the massive steel design lacks concrete fillings, which ensures an outstanding durability. The modular design also allows the machine to be divided into sections for easy transportation.
Cooling
The Video of the 42 Meters Casting Cooler
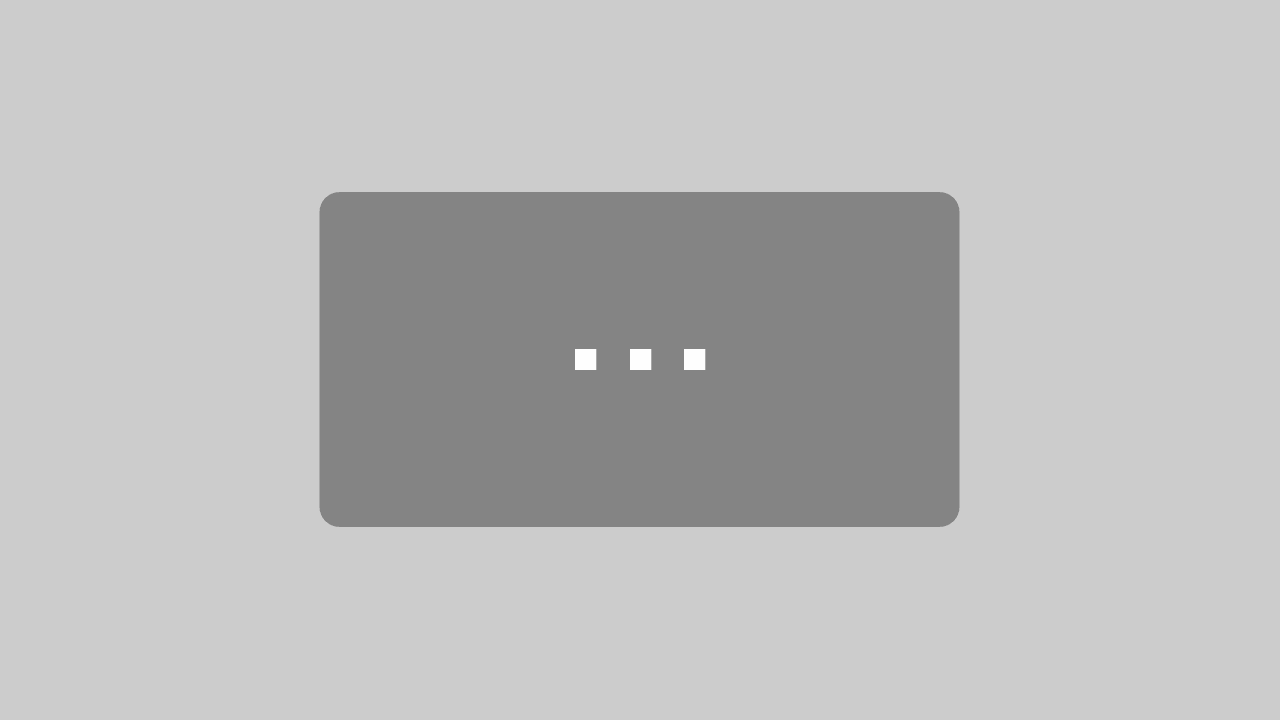
We need your consent to use the YouTube service!
More Information
Weitere Beiträge
As part of the JOEST group, MOGENSEN has been a trusted provider of high-performance screening and sorting technologies for many years. The new website now showcases this expertise more clearly and with a modern touch.
On International Women’s Day, we celebrated the great women in our company who have made a significant contribution every day with their commitment, expertise and passion. Their efforts have been a driving force behind our success and an inspiration to us all.
JOEST South Africa was commissioned to manufacture and supply replacement vibrating feeders for a critical power generation facility. The new units are designed to replace equipment that had been in operation for over 20 years, ensuring the continued reliability and efficiency of the plant.
MOGENSEN joins China’s food security project as an official supplier, supporting the nation’s plans to strengthen domestic grain production capabilities. The appointment by COFCO, China’s largest state-owned agricultural company, includes the deployment of multiple precision screening systems for processing rice, wheat and soybeans, among other grains. This long-term initiative is in line with China’s new food security law, which went into effect on June 1, 2024.