COLD FORMING
Fully automated de-oiling, washing, cleaning and drying of
screws - within a singel system
Dr. Goessling supplies wash centrifuge for baier & michels, specialists in joining technology.
Maximal throughput when de-oiling and cleaning screws or small parts of various dimensions: Dr. Ing. Goessling Maschinenfabrik GmbH, a subsidiary in the JOEST Group, took on this challenge in a joint effort with baier & michels GmbH & Co. KG, based near Frankfurt. This global player with over 400 employees has specialized in the development and production of innovative joining parts and C-part management for the automotive industry. In addition to the preexisting relationship with the client, Dr. Goessling convinced with high quality and a matching system, the washing centrifuge WZ550.
The wash centrifuge WZ550 is an inline cleaning machine that uses a patented process to de-oil and clean mass parts. All steps of the process are performed in sequence within the plant, avoiding the need to extract the parts throughout the process. Furthermore, parameters can be adjusted to change the cleaning result according to the client’s demands. The wash centrifuge consists of a portable base with three identical washing drums that are arranged in a plain. The lids, that vary from station to station, are fixed.
“The task we gave Dr. Goessling was to design a plant that could clean parts up to a size of M14x100 and a weight of 100 g in a gentle fashion, after they have been pressed or rolled. It was also very important to recover the oil that sticks to the parts after pressing or rolling and returning it to the process. This was achieved to perfection in this plant, allowing us to uphold our high product standards in the area “product cleaning” as well.” – Olaf Ambros, Head of Technology & Development at baier & michels
An apron conveyor with a built-in scale feeds the parts into the first centrifuge. The apron conveyor prevents the parts from getting trapped or hooked and thus results in an even distribution of material. In the first step the oil is separated from the parts by centrifuging them at up to 1,000 rpm, collecting the oil in a surrounding housing. From here, the oil is drained off through hoses and can either be collected in containers or directly inserted into a further process. After each step, the turn table the centrifuges are mounted to, is rotated by 120°C for the next step.
During the second step, the mostly oil free material is washed with warm suds at up to 80°C. This also acts as corrosion prevention. Afterwards the material is centrifuged once again, removing excess suds and drying it in the process.
In the third and last step, the material is rinsed to remove all remaining suds. It is then centrifuged again, dried with warm air of up to 350°C and emptied into a container. An intervening flap and vibrating slide allow for gentle conveying into the container. To prevent damage to the material, the funnels and vibrating slides are lined with Vullkolan. A full cycle with the product provided by baier & michels takes roughly 85 sec. The steps are repeated until all of the parts have been cleaned and fed into containers.
A water purification unit is set up alongside the wash centrifuge to seamlessly provide water and suds. It processes the washing suds, removing any remaining oil with an oil extractor and filling it into a tank for reuse. The washing suds tank holds 2,000 l and the rinsing tank holds 1,000 l of fresh water. Both fresh water and washing suds are automatically refilled. Since 95% of the oil sticking to the material is separated in the first step, a carryover of oil is avoided. The water purification and automatic refill function enable a long lifetime of the washing solution. All inlets, outlets and pumps of the unit are fitted with filters that collect debris such as metal shavings from the fluid circuits. This eliminates causes of damage and significantly reduces maintenance.
A high material throughput, clean result and very little loss of water and suds during a cycle make the WZ550 stand out. When evenly charged, the WZ550 is designed for a material throughput of up to 1,000 kg per hour, depending on the materials bulk mass bulk mass. It can clean small and large parts with diameters ranging from 5 mm to 100 mm, lengths between 5 mm and 150 mm and even complex geometries with unit weights of up to 230 g. Materials such as steel, stainless steel, aluminum and also non-ferrous metals can be processed. The unit designed for baier & michels features a maximum throughput of 800 kg per hour, cleaning parts of up to 100 g and 100 mm in length per piece. The patented process enables an oil recovery of 95% which can then be reused, drastically reducing oil disposal fees in comparison to other systems. An additional advantage is the unit’s compact design: roughly 10 m² of floorspace are required. A smooth operation is provided thanks to a very effective vibration damping system.
Installation and commissioning at baier & michels was performed by Dr. Goessling. Both worked out seamlessly and to the full satisfaction of the client, as did all prior cooperation. Dr. Goessling managed to extend the good relationship and build on the clients trust. They are looking forward to future projects.
The wash centrifuge featured here is also available in a smaller edition, the WZ350. The extensive product portfolio also features pure de-oiling centrifuges. These also implement the small form factor which makes them easy to integrate into any existing production. Complete solutions can be complemented by the extensive portfolio of bulk material handling machines offered by the JOEST group Dr. Goessling is part of since 2019.
The wash centrifuge WZ550 in use at baier&michels:
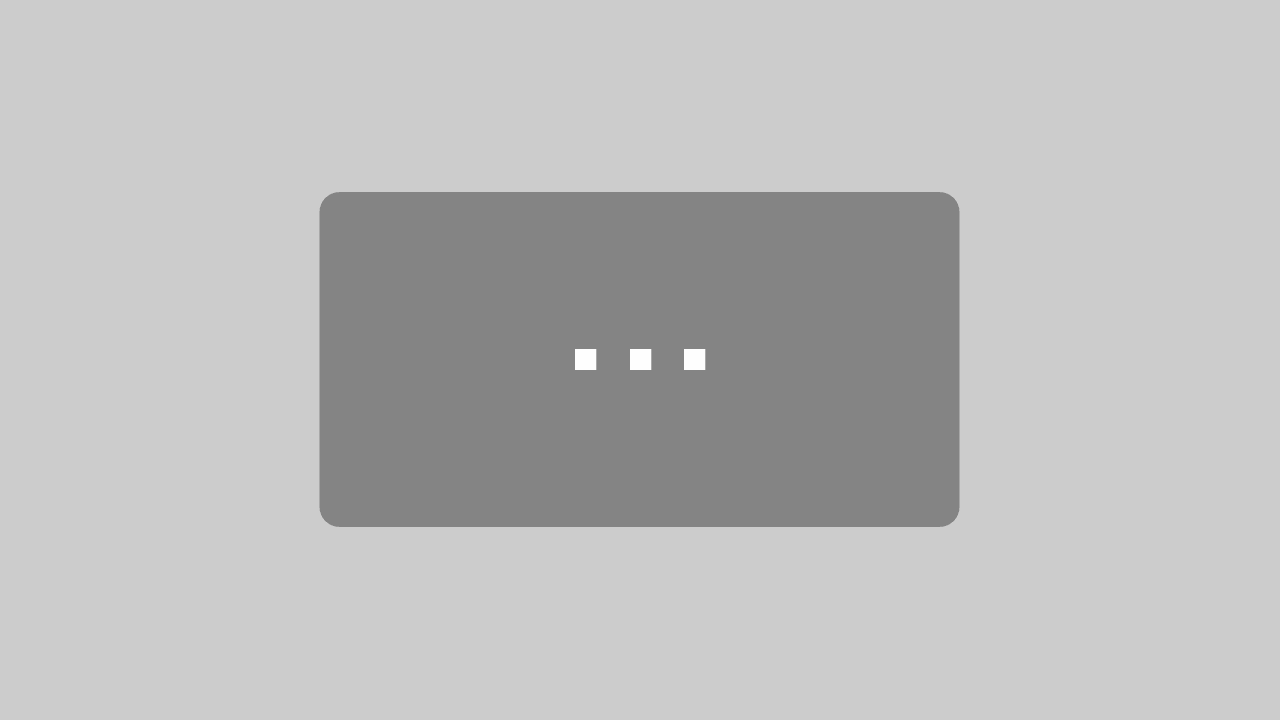
We need your consent to use the YouTube service!
More Information
Weitere Beiträge
As part of the JOEST group, MOGENSEN has been a trusted provider of high-performance screening and sorting technologies for many years. The new website now showcases this expertise more clearly and with a modern touch.
On International Women’s Day, we celebrated the great women in our company who have made a significant contribution every day with their commitment, expertise and passion. Their efforts have been a driving force behind our success and an inspiration to us all.
JOEST South Africa was commissioned to manufacture and supply replacement vibrating feeders for a critical power generation facility. The new units are designed to replace equipment that had been in operation for over 20 years, ensuring the continued reliability and efficiency of the plant.
MOGENSEN joins China’s food security project as an official supplier, supporting the nation’s plans to strengthen domestic grain production capabilities. The appointment by COFCO, China’s largest state-owned agricultural company, includes the deployment of multiple precision screening systems for processing rice, wheat and soybeans, among other grains. This long-term initiative is in line with China’s new food security law, which went into effect on June 1, 2024.