COLD WORKING
Oil recovery up to 95%
with the Washing Centrifuge
by GOESSLING
De-oiling, washing, cleaning and drying in a single machine
In the fall of last year, the Dr. Ing. Goessling Maschinenfabrik GmbH, a subsidiary of the JOEST group, delivered the Washing Centrifuge WZ550 to the client baier & michels GmbH & Co. KG. The company based near Frankfurt with over 400 employees is a specialist for the development and production of innovative joining parts and c-part management for the automotive industry.
The patented process of de-oiling and cleaning mass production components enables the inline cleaning machine to achieve an oil recovery of up to 95%. Three identical drums are mounted to a rotating frame, in which the process steps de-oiling, washing, cleaning and drying are performed in sequence. It is therefor not necessary to empty the drums in-between steps. The lids, which vary from step to step are fixed.
The existing machine is charged by a Hinged Belt Conveyor with an integrated scale, which is also part of the Dr. Goessling product portfolio. The majority of the oil is separated in the first step by centrifuging the parts at up to 1.000 RPM. The oil is collected and then either stored in containers or directly fed into a new process.
For an optimal result, the mostly de-oiled material is washed with warm suds of up to 80°C. This also acts as a corrosion prevention. Bevor the material enters the last step, it is centrifuged once again to remove the washing suds.
In the last step, the material is rinsed to get rid of any remaining suds. It is then dried with hot air of up to 350°C. The drum is completely emptied into a container. After each step, the frame mounting the drums is rotated by 120° to move the parts to their next processing station. This is done fully automatic, and the timing can be adjusted based on the amount material.
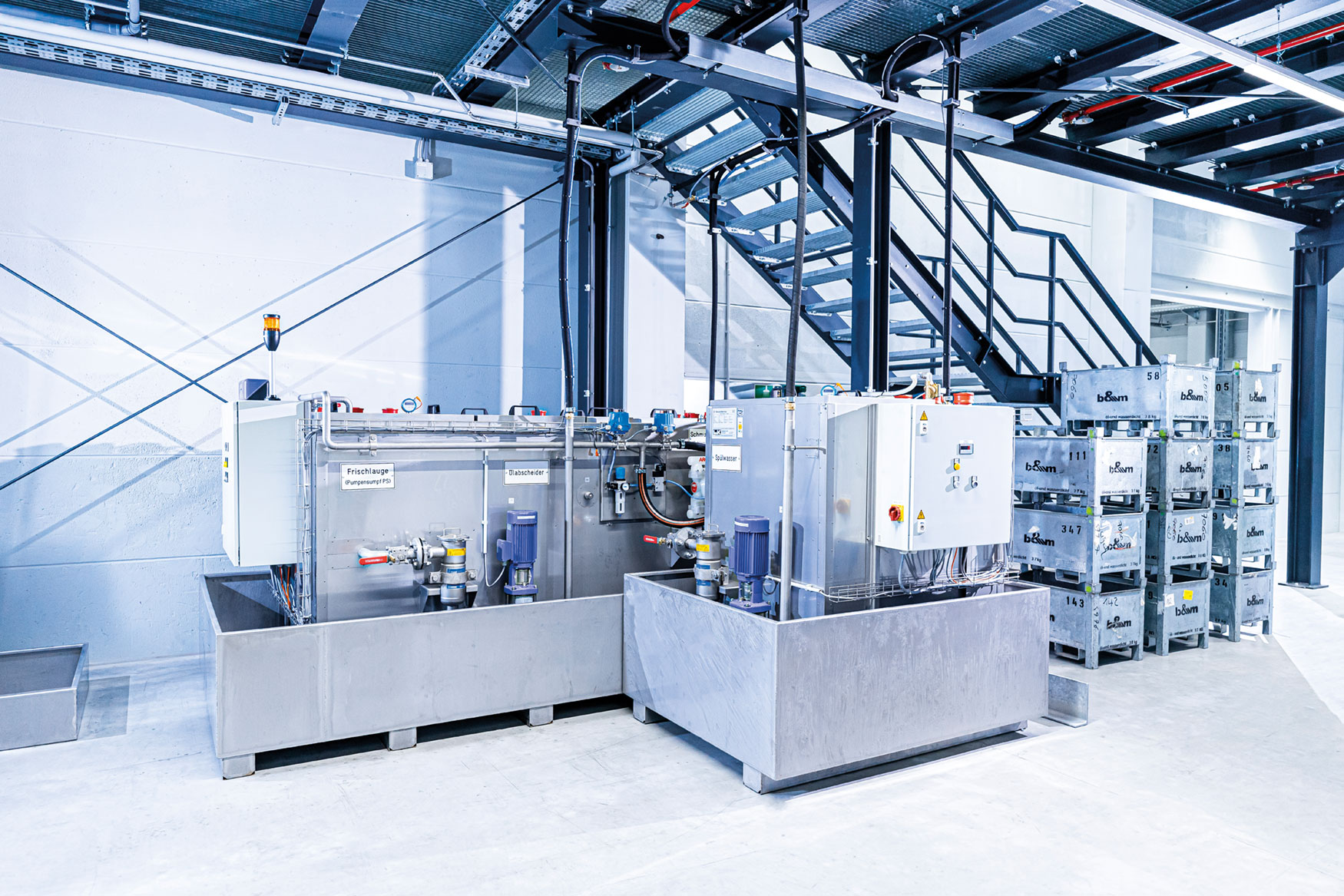
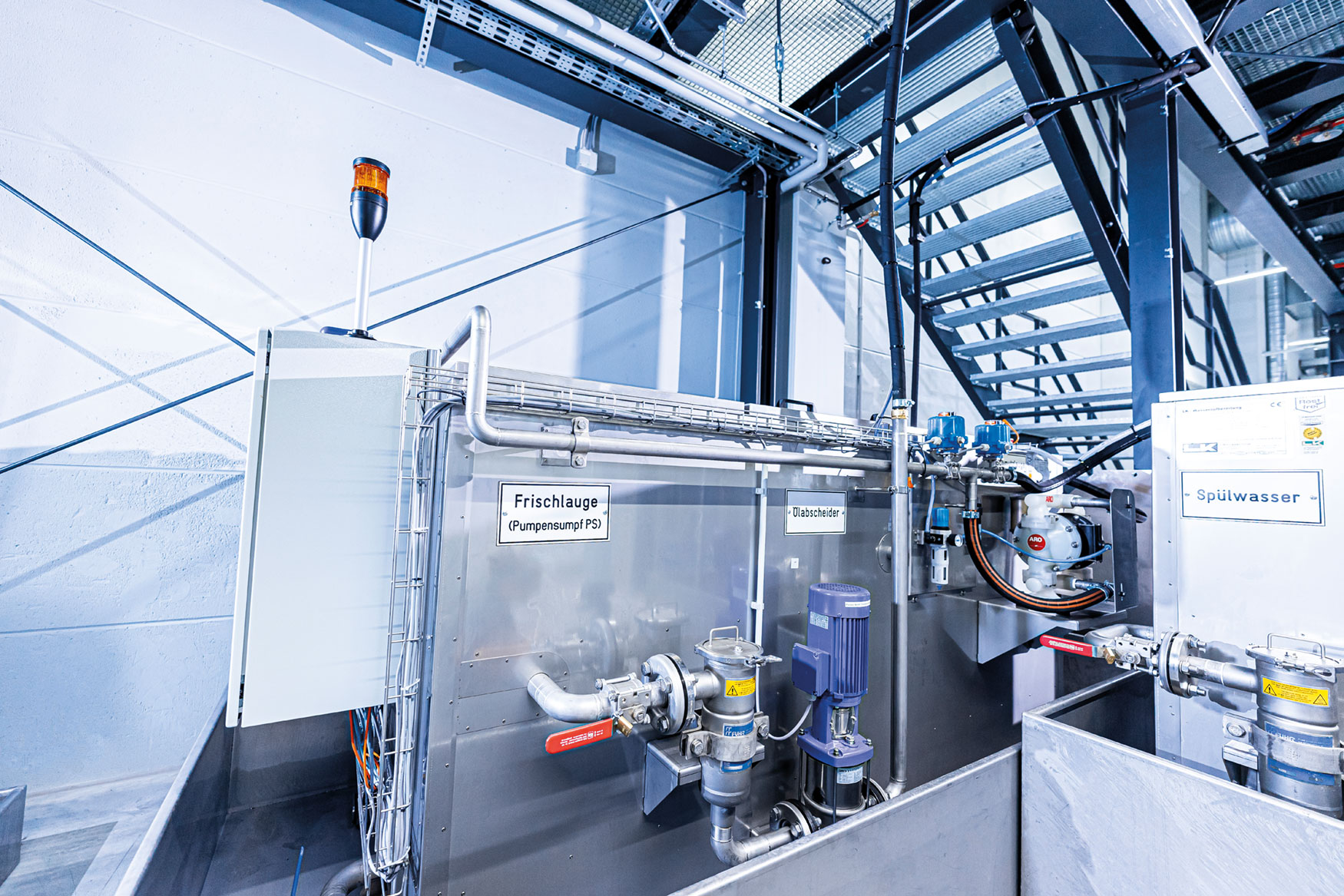
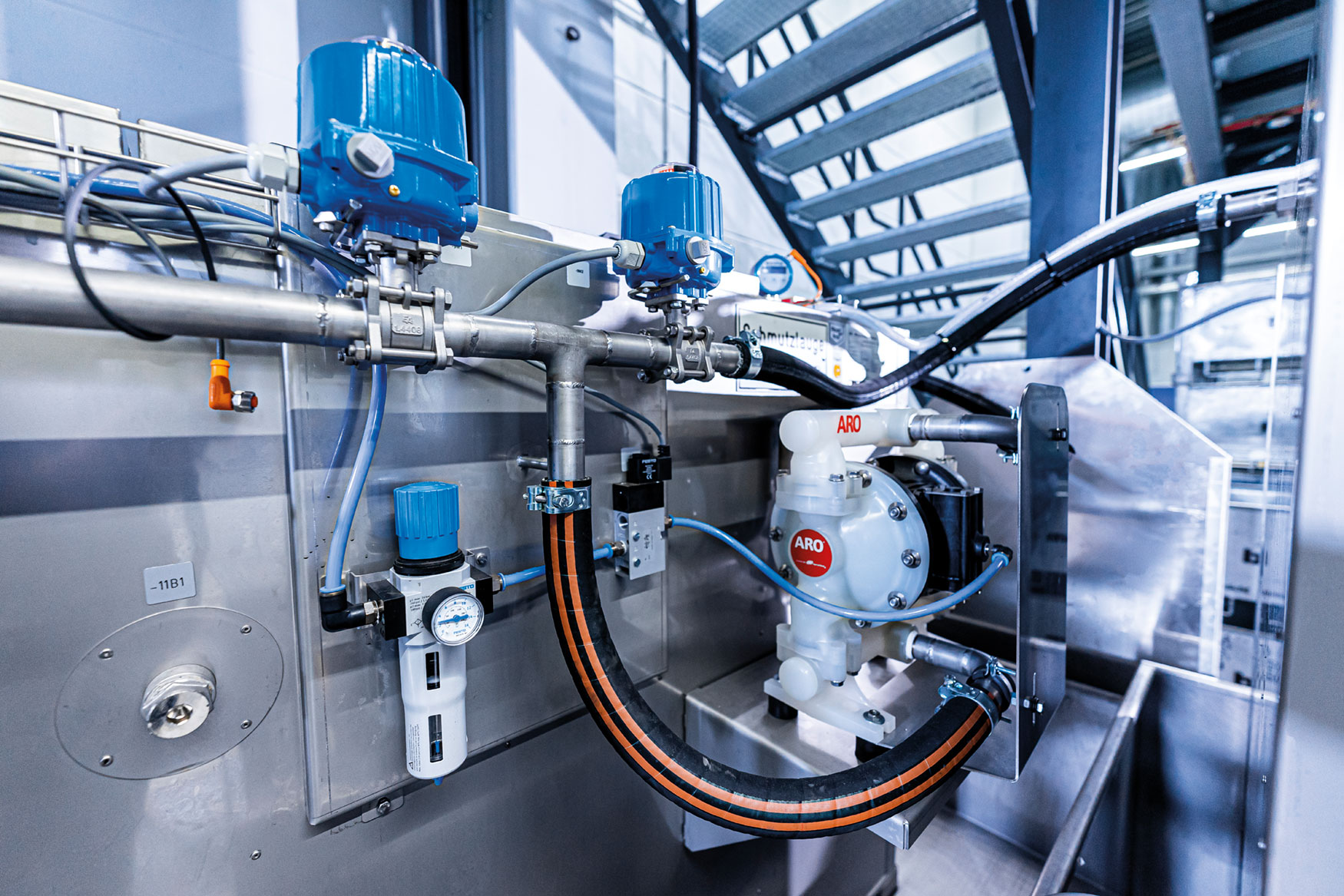
The Washing Centrifuge WZ550 has a maximum throughput of 1.000 kg per hour when filled evenly and depending on the parts’ apparent weight. Small and Large parts with various geometries and weights of up to 230g each can be cleaned. The very clean result and the minimal carry-over of suds, water and oil enable the reusability of the oil and drastically reduce oil disposal fees when compared to other machines.
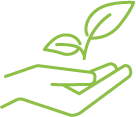
This way the Washing Centrifuge also helps meet the increasingly strict demands of the environmental certification ISO 14001. Another key feature is its compact form factor: the necessary surface area is only 10 m².
In its wide product spectrum, Dr. Goessling also offers mere de-oiling centrifuges that are used for oil recovery too, as well as numerous conveyors. This is complemented by the broad product portfolio of the JOEST group, which the Dr. Ing. Goessling Maschinenfabrik GmbH is a part of since 2019.
“This was achieved to perfection in this plant, allowing us to uphold our high product standards in the area "product cleaning" as well.“
WZ550
Video of the Washing Centrifuge
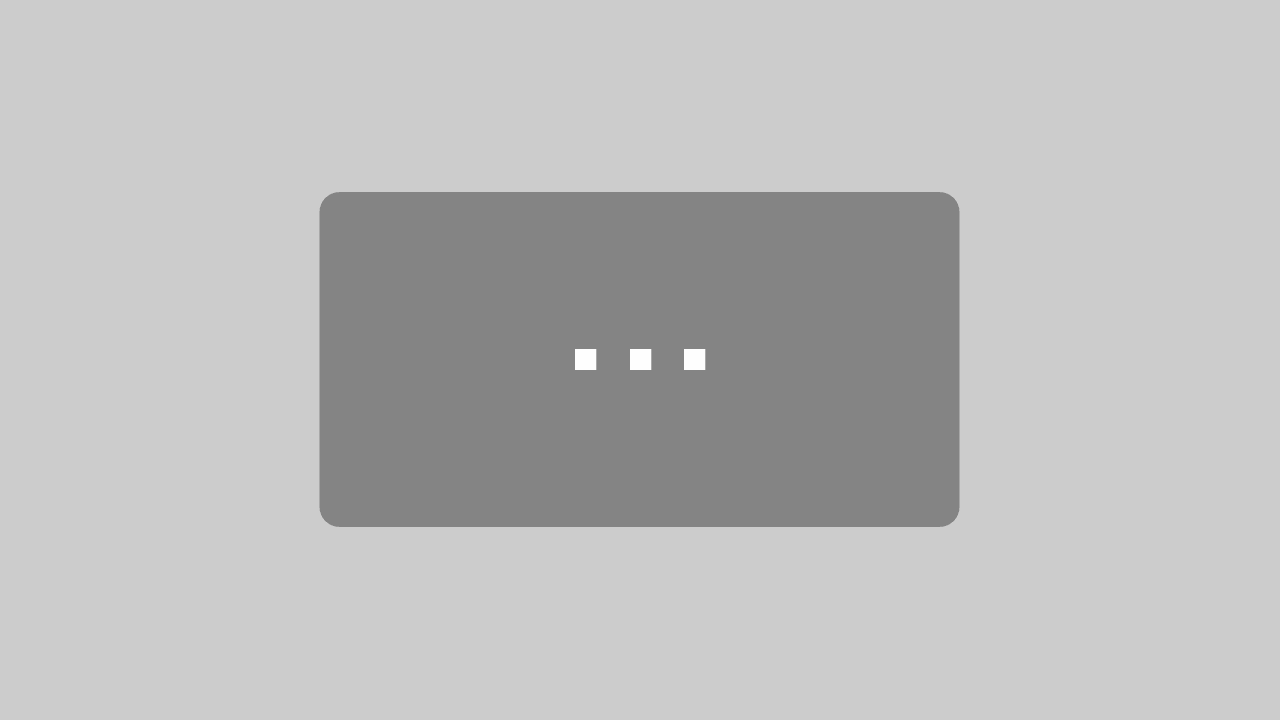
We need your consent to use the YouTube service!
More Information
Weitere Beiträge
As part of the JOEST group, MOGENSEN has been a trusted provider of high-performance screening and sorting technologies for many years. The new website now showcases this expertise more clearly and with a modern touch.
On International Women’s Day, we celebrated the great women in our company who have made a significant contribution every day with their commitment, expertise and passion. Their efforts have been a driving force behind our success and an inspiration to us all.
JOEST South Africa was commissioned to manufacture and supply replacement vibrating feeders for a critical power generation facility. The new units are designed to replace equipment that had been in operation for over 20 years, ensuring the continued reliability and efficiency of the plant.
MOGENSEN joins China’s food security project as an official supplier, supporting the nation’s plans to strengthen domestic grain production capabilities. The appointment by COFCO, China’s largest state-owned agricultural company, includes the deployment of multiple precision screening systems for processing rice, wheat and soybeans, among other grains. This long-term initiative is in line with China’s new food security law, which went into effect on June 1, 2024.